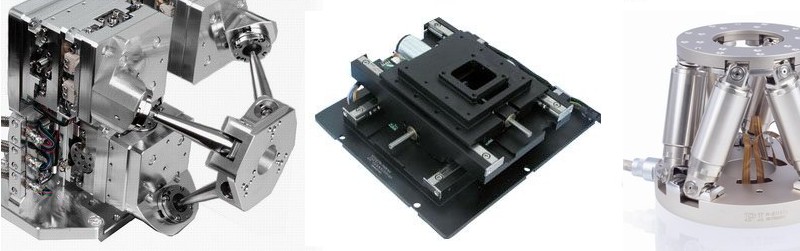
6-Axis Stages, XY-Tables, XYZ-Stages, XYZ-Gantries,
Multi-Axis Stages for Motion Control
Multi-axis stages, such as hexapod 6-axis stages and XYZ Gantry stages are often used in for precision alignment of optics, photonics components, lasers, semiconductors, and precision mechanics. For less complex motion applications, 2-axis, 3-axis linear stages and 4 and 5-axis combinations of linear XY-tables, XYZ-stages and rotary and goniometer stages are sufficient. PI postioning stages and precision motorized 3-axis gantries and split bridge stages are designed for precision motion control applications from photonics alignment to medical design and semiconductor related test and manufacturing processes. In addition to standard single-axis, XY, XYZ and multi-axis stages with mechanical bearings. air-bearing stages and high vacuum stages are also available.
|
![]() 9-Axis Granite Bridge Motion System with XY-Linear Motor Stage, Hexapod 6-Axis Stage and Z-stage. More on Multi-Axis Custom Granite Motion Systems |
![]() |
![]() | |||||||
6-Axis Stages - Hexapods | 2-Axis Stages, 3-Axis Stages, Multi-Axis Stages | |||||||
![]() | |||||||
XY, XYZ and Multi-Axis Positioning Stages | |||||||
![]() | |||||||
10-Axis Custom Stage for Test / Precision Manufacturing | |||||||
This high performance 10-axis stage for test and metrology, in high precision industrial automation is an example of PI's custom motion control systems design capabilities. 10 Axis Stage and other Multi-Axis Systems for Automation: Specifications and more Information |
![]() | ||||||
![]() | |||||||
![]() More information on Motorized XYZ-Gantry Stages with High Precision |
Motorized XYZ Gantry - Precision
|
||||||
![]() | |||||||
![]() Read article on Custom 3-Axis Motorized XYZ-Linear Stages - Tuned and Assembled |
Motorized Custom Tuned XYZ Linear Stages
|
||||||
![]() | |||||||
Video: Motorized Precision Gantry Stage for Additive Manufacturing for 3-Axis Precision Motion, Direct-Drive Linear Motors | |||||||
![]() |
Video: Compact 3-Axis Linear Stage with Air Bearings, Nanometer Resolution, for Photonics Alignment, Sample Scanning, Precision Assembly - High Duty Cycle, Zero Maintenance, Wear-Free | ||
![]() |
Video: 5-Axis Precision Positioning Stage with Air Bearings, for Semiconductor Processing based on a planar X-Y Air Bearing Table and a 3-Axis, Z-Tip/Tilt (Z / Theta-X / Theta-Y) Air Bearing Table. |
![]() |
Integrated XY-Tables. Linear Motors and Ball-Screw Options | ||
These two axis XY-tables are available with aperture, with linear motors or ball-screw drives, and are designed for high precision industrial automation. XY-Linar Tables - more information |
![]() |
![]() |
5-Axis Granite Stage - Split Bridge Design | |||||||
Granite-based stage designs provide high stability and precision. PI can quickly provide design concepts for gantry-type Cartesian robot designs and split bridge granite motion systems. Stages with mechanical bearings and air bearings are available for integration. |
![]() |
![]() |
U-751/ M-686 XY-Table with Precision Piezo Linear Motors & Linear Encoders | ||
These open-frame micro-positioning XY-stages (XY-tables) are designed for life-science and microscopy applications. If nanometer precision is required, a piezo flexure stage can be mounted on top. PDF Brochure | XY-Stage Specifications, Drawings, Answers to Technical Questions |
![]() |
![]() |
OEM Integrated XY-Table for Micropositioning and Scanning | ||
![]() |
Fast XY positioning table with precision guiding system: the M-900KOPS planar scanner was developed for OEM applications / white light interferometetry PDF Brochure | XY-Tables Specifications |
![]() | ||
M-880 XY-Theta 3-DOF Planar Precision Micropositioning Positioning Stage Concept | ||
|
![]() |
![]() |
Precision XY-Table for High-Resolution Microscopes | ||
![]() |
PI XY-tables / microscope stages are designed for excellent thermal and positional stability. PILine® piezomotor-driven stages excel in precision positioning and automation applications. The low profile height makes integration easy and a choice of mechanically compatible high-resolution PI piezo nanopositioning / scanning stages adds to the versatility. PDF Brochure | XY-Stages for Microscopy Information |
![]() |
M-545 XY-Table for Microscopy: Manual & Motorized | ||
This XY micropositioning stage is designed to provide a stable platform for PInano® piezo nanopositioning and scanning stages as well as other PI nanopositioning stages PDF Brochure | XY-Stage for Microscopy Specifications, Drawings, Answers to Technical Questions |
![]() |
![]() |
Multi-Axis Precision Positioning Sub-Systems | |||||||
![]() |
A variety of multi-axis sub-systems is available to solve precision motion and automation needs. Multi-Axis Subsystems overview |
![]() |
XYZ Stage for Photonics Alignment | ||
The F-131 3-Axis stage is a compact computer-controllable XYZ precision positioning / nanopositioning system for precision alignment application such as fibers / optical components. The coarse positioners provide 50 nanometers resolution, enough to find first light and the piezo fine drives provide 1 nanometer and very fast response for quick scanning. Watch youtube video at http://www.youtube.com/v/mwQlxUDvAgI PDF Brochure | XYZ Stage Specifications, Drawings, Answers to Technical Questions |
![]() |
![]() |
N-510 3-Axis Z/Tip/Tilt Platform, Ultra-High Precision for High Loads | ||
![]() |
PDF Brochure | Z-Tip/Tilt Platform Specifications, Drawings, Answers to Technical Questions |
![]() |
H-810 Miniature 6-Axis Stage - 6-DOF Motorized Hexapod Platform | ||
![]() |
This miniaturized precision 6-DOF hexapod platform is currently PI's smallest standard 6-axis micropositioning system to date (smaller custom systems are available). As all PI hexapod platforms it allows the user to change the center of rotation (pivot point) anywhere inside or outside the system envelope. PDF Brochure | 6-Axis Stage Specifications, Drawings, Answers to Technical Questions |
![]() |
![]() |
![]() |
H-811 6-Axis Stage - Vacuum-Compatible Miniature Hexapod 6-DOF Positioner; High Precision and Very Versatile
- Vacuum-Compatible Miniature 6-DOF Stage Hexapod
- Complete with Specialized Hexapod Controller and Software
- Travel Ranges 34 x 32 x 13 mm, Rotation to 42 Degrees
- Load Capacity to 5 kg
- Actuator Resolution 40 nm
- Min. Incremental Motion to 200 nm
- Repeatability up to ±0.2 µm
- Velocity to 10 mm/sec
PDF Brochure | 6-Axis Stage Specifications, Drawings, Answers to Technical Questions
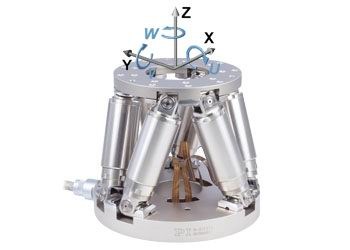

H-824 6-Axis Stage - Compact 6-DOF Hexapod Platform
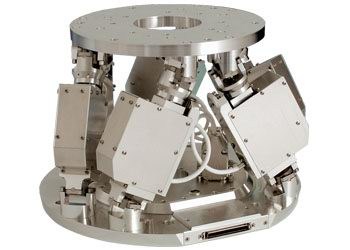
- 6-axis stage with Nanometer Resolution Actuators
- Arbitrary Center of Rotation
- Vacuum Option
- Load Capacity 10 kg
- Motorized Positioning Range to 45mm (linear), 25° (rotation)
- 300 Nanometer Min. Incremental Motion ±0.5 Micron Reproducibility
- Self Locking to 10 kg
- Sophisticated Controller Using Vector Algorithms
This hexapod 6-dof platform combines compact dimensions with high accuracy and load capacity. A vacuum version is available.
PDF Brochure | 6-Axis Stage Specifications, Drawings, Answers to Technical Questions
H-850 6-Axis Stage - High Load 6-DOF Platform - Parallel Kinematics
- Up to 250kg Load Capacity
- Actuator Resolution to 0.005 Microns
- Arbitrary Center of Rotation (Pivot Point)
- Works in Any Orientation
- No Moving Cables = Higher Reliability & Precision
- Heavy-Duty, Ultra-High-Resolution Bearings for 24/7 Applications
- Reproducibility to ±1 Micron
- Smaller & Stiffer Package than Conventional Multi-Axis Positioners
- Vacuum-Option
- Sophisticated Controller Using Vector Algorithms
- 20000 h MTBF
The H-850 is the ideal micropositioning system for all complex positioning tasks which depend upon high load capacity and high accuracy in six independent axes. Extremely stiff & accurate components provide an very high natural frequency of 500 Hz with a 10 kg load. As all PI hexapod platforms it allows the user to change the center of rotation (pivot point) anywhere inside or outside the system envelope.
Several models with brushless and standard motors are available to cover different velocity and load ranges.
PDF Brochure | 6-Axis Stage Specifications, Drawings, Answers to Technical Questions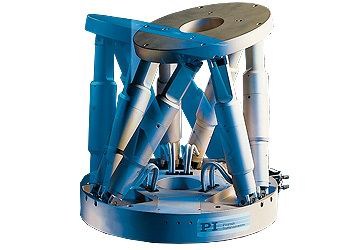

H-840 Fast Six Axis Stage - Parallel Kinematics 6-DOF Hexapod Platform
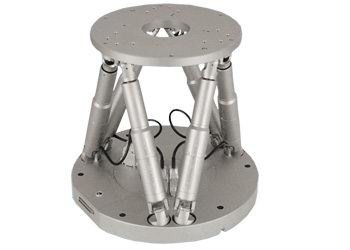
- 6-Axis Motion Stage
- Actuator Resolution to 0.016 Micron
- Rapid Response
- Motorized Positioning Ranges to 100mm/ 60°
- No Moving Cables = Higher Reliability and Precision
- Self-Locking Option to 30kg Load
- Fast Direct-Drive Option to 50mm/second
- Vacuum-Option
- Arbitrary Center of Rotation (Pivot Point)
- Sophisticated Controller Using Vector Algorithms
- 20000 h MTBF
The H-840 is a high-accuracy, mid-size, 6-DOF hexapod micro-positioning system for all complex positioning tasks which rely on high accuracy and speed in six independent axes. In addition to positioning all axes, it allows the user to define the center of rotation (pivot point) anywhere inside or outside the system envelope by one simple software command.
PDF Brochure | 6-Axis Stage Specifications, Drawings, Answers to Technical Questions
H-206 6-Axis Stage for Precision 6-DOF Alignment, 6-Axis Manipulator
- 6-DOF Parallel Kinematics Manipulator
- Constant-Length Strut Design w/ Friction-Free Flexure Guides
- 33 Nanometers Actuator Resolution
- Reproducibility 0.3 Micron in Space
- No Moving Cables = Improved Reliability & Reduced Friction
- Better Dynamics, More Compact than Serial Kinematics Systems
- For Scanning and Alignment
- Cartesian Coordinate Control with Virtualized Pivot Point.
- Powerful Digital Controller with Open Source LabView™ Drivers, DLL Libraries...
- Integrated Fiber Alignment Routines
This compact 6-DOF Hexapod platform is a highly accurate micro- positioning system for complex multi-axis alignment tasks. It is based on PI"s long experience with ultra-high-resolution, parallel kinematics stages. The use of constant-length struts w/ backlash & friction-free flexure guides (as opposed to variable-length struts) gives the F-206 even higher precision than other hexapod designs.
PDF Brochure | 6-Axis Stage Specifications, Drawings, Answers to Technical Questions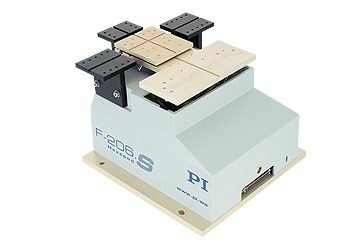

More Multi-Axis Parallel Positioners / SpaceFABs from PI miCos
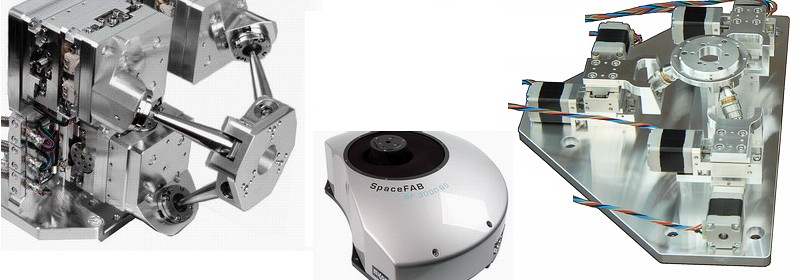





Mini Positioners
![]() |
Piezo Positioners
![]() |
Precision Actuators
![]() |
Multi-Axis Positioners
![]() |
![]() Linear Stages, Vertical Positioners |
![]() Rotation Stages |
![]() Motion Controllers |
![]() Nanopositioning |
||||